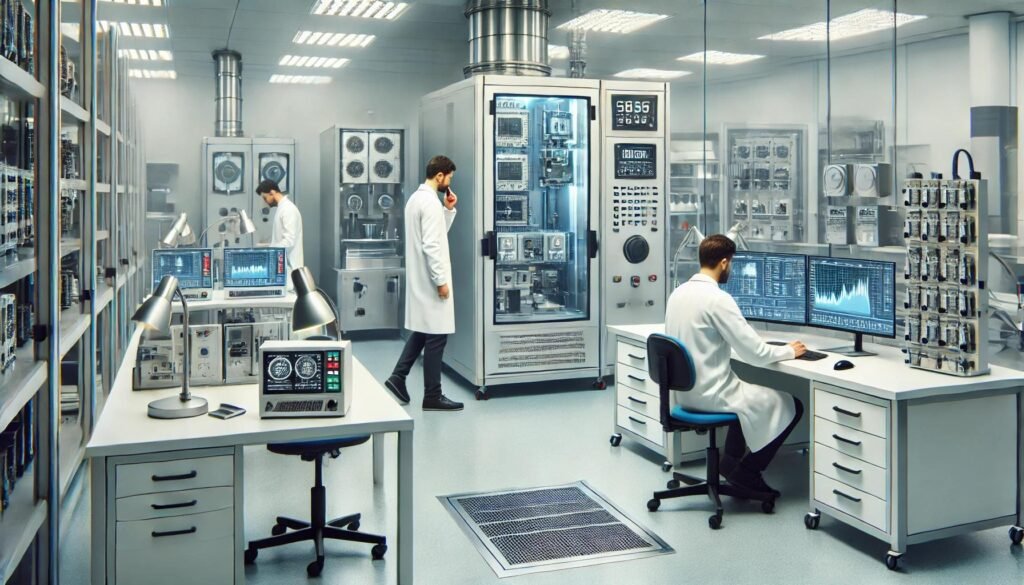
Guide to PEM Qualification Testing Services
Plastic Encapsulated Microcircuits (PEMs) are essential in modern technology, offering compact, cost-effective solutions across industries such as aerospace, defense, automotive, and consumer electronics. Ensuring their reliability in demanding environments requires rigorous qualification testing. This guide will help you understand and utilize PEM qualification testing services effectively.
What is PEM Qualification Testing?
PEM qualification testing evaluates the reliability, durability, and performance of plastic encapsulated microcircuits under real-world stresses. This process ensures these components are fit for high-stakes applications.
Read More: Guide to Psychological Testing in Boca Raton
Key Features of PEM Qualification Testing
Feature | Description | Cost Range (Approx.) |
---|---|---|
Screening | Initial testing to detect and eliminate defective units. | $1,000–$5,000 per batch |
Qualification Testing | Comprehensive evaluation of PEMs under simulated operational conditions to assess their long-term reliability. | $10,000–$50,000 per project |
Destructive Physical Analysis (DPA) | In-depth analysis involving disassembly to inspect internal structures for potential failure mechanisms. | $5,000–$15,000 per component |
Failure Analysis (FA) | Identifying the root cause of failure in defective components, enabling improvements in design or materials. | $3,000–$10,000 per analysis |
Thermal Cycling | Testing components under repeated temperature fluctuations to evaluate their thermal fatigue resistance. | $2,000–$7,000 per batch |
Environmental Stress Testing | Subjecting components to extreme environmental conditions (e.g., temperature, humidity) to ensure durability. | $2,000–$10,000 per test cycle |
Electrical Testing | Verifying electrical performance under different operating conditions to meet specifications. | $1,500–$8,000 per batch |
Read More: Six Flags Over Georgia: Rides, Costs, Reviews
Step-by-Step Guide to PEM Qualification
Step 1: Define Objectives
- Identify the specific operational and environmental conditions the PEMs will face.
- Establish reliability benchmarks and performance requirements.
Step 2: Choose the Right Service Provider
- Look for providers with expertise and adherence to industry standards like MIL-STD-883 and SAE AS6294.
- Examples of reputable providers include:
- Integra Technologies for reliability testing.
- ORS Labs for destructive physical analysis.
- Micross Components for up-screening and qualification services.
Step 3: Conduct Screening
- Perform initial tests to identify and eliminate defective components.
- Include visual inspections, basic electrical tests, and environmental stress testing.
Step 4: Perform Qualification Testing
- Simulate operational conditions to evaluate reliability.
- Conduct thermal cycling, vibration tests, and accelerated life testing.
Step 5: Execute Destructive and Failure Analyses
- Use Destructive Physical Analysis (DPA) to inspect internal structures and materials.
- Conduct Failure Analysis (FA) to diagnose root causes of component failures.
Step 6: Finalize Testing and Report Findings
- Prepare a detailed report summarizing results, insights, and recommendations.
- Share findings with stakeholders to guide improvements in design or materials.
Read More: How to Change Text in Images with AI
Benefits of PEM Qualification Testing
- Enhanced Reliability: Ensures components meet rigorous performance and reliability standards.
- Cost-Effectiveness: Reduces the likelihood of costly field failures by identifying issues early.
- Compliance Assurance: Helps meet industry-specific standards, critical for aerospace and defense.
- Extended Lifespan: Identifies potential weaknesses to improve durability and performance.
Frequently Asked Questions (FAQs)
Why is PEM qualification testing important?
PEM testing ensures that components can withstand operational and environmental stresses, minimizing failures in critical applications.
What industries require PEM qualification testing?
Industries like aerospace, defense, automotive, and consumer electronics rely heavily on PEM qualification testing to ensure reliability.
What are common testing methods in PEM qualification?
Key methods include thermal cycling, electrical testing, environmental stress testing, and destructive physical analysis.
How do I choose a PEM testing service provider?
Look for providers with experience, adherence to industry standards, and a track record of delivering accurate, reliable results.
Is PEM qualification testing expensive?
Costs vary based on the complexity of the tests, ranging from $1,000 for basic screening to $50,000 for comprehensive qualification testing.
What standards govern PEM qualification testing?
Key standards include NASA’s PEM-INST-001, MIL-STD-883, and SAE AS6294, which outline testing requirements for reliability and compliance.
Conclusion
PEM qualification testing is essential for ensuring that microcircuits perform reliably in demanding applications. By following the outlined steps, selecting the right service providers, and investing in comprehensive testing, organizations can minimize risks, enhance reliability, and ensure compliance with industry standards. This investment not only improves product quality but also boosts customer confidence and market competitiveness.